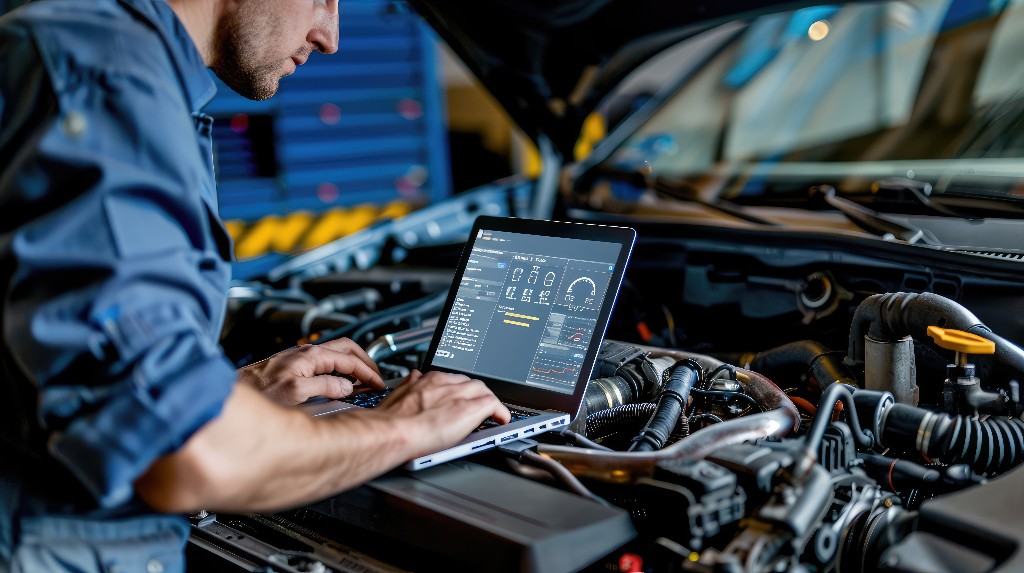
Featured image for "How Vehicle Inspection Tools Can Reduce Comebacks"
Aren’t comebacks a bummer? It’s such a buzzkill when you did a good job inspecting the vehicle and taking care of the repairs, only for the customer to return with a complaint. Almost every auto repair shop struggles with comebacks now and then. When this happens, how do you decide who will be responsible for it? You might start losing money fast when your technicians are questioned about “how well the job was done?”
While experts are on hand to fix whatever is wrong with the vehicle, AI-powered tools can be more helpful. A tool that takes over vehicle inspection on a technician’s behalf can improve the overall process. An auto repair shop with a streamlined workflow uses smart vehicle inspection tools for further evaluation.
How?
Let’s take a closer look at how such tools can reduce comebacks and also improve the overall efficiency of vehicle inspections and repairs.
Why comebacks occur
There are multiple reasons why comebacks can occur. The most common reasons are:
Broken workflow
The first major point of concern for any auto repair shop is its workflow. Many might not like the idea, but it can be true at times. Any error in the existing workflow can result in loss of time, productivity, and several complaints (and comebacks).
A broken workflow, such as a lack of space, a slow inventory reordering process, or lots of time breaks for coffee or smoking, can be a root cause for inadequate inspection. Or perhaps the reason a technician might be distracted and not focusing on the task at hand.
For instance, a car delivered to the customer suffers an epic engine failure because the disintegrated water pump issue wasn’t taken care of in the first place. Hence the comeback.
Lack of training
Each comeback is expensive, costing you time and money, and a frustrated customer. If a technician fails to understand a customer’s concern, then they fail miserably. A wrongly inspected vehicle is one of the most common causes of comebacks.
Another reason can be the lack of proper training for the employees at hand. A workshop owner must train their technical staff about new vehicles, new technology being used in the shop, and how to ensure a quality check.
Unable to handle challenging situations
Another common issue is that technicians or the technical staff try to handle the challenging issues on their own. While they might be expert with the car’s engine and can locate the real root cause, handling a paranoid customer might not be their strongest suit. Mechanics are reluctant to guide customers about the diagnostic issues because they can be looked over as inexperienced or unprofessional.
Also, sometimes shop managers fail to discuss comebacks with the technician, which can lead to pointing fingers and dismissal of serious concerns.
What are car inspection tools?
Any auto repair shop is proud of two things: its manpower and the tools invested in. The right choice of vehicle inspection tools enables them to keep a clean bill of the cars’ health and track their performance too. Digital vehicle inspection helps track other metrics as well, such as in-house and outhouse repairs, check off tasks, etc, in detail, making sure everything is available at a whim of a click.
Having high-quality vehicle inspection tools (which are also affordable) makes it a lot easier to manage repairs, improve workflow efficiency, and reduce the number of comebacks.
An in-depth vehicle inspection is mostly mechanical. Previously, it used to take more than a day, two at max, for a thorough inspection. But now the use of modern digital tools has made it a piece of cake, such as the use of:
- Laptop
- Cloud-based software
- A tachometer
- All the necessary tools
- OBD-II scanner or a code reader
- Camera systems
How vehicle inspection tools reduce comebacks
According to a survey, a comeback can cost around $250-$400 on average. However, modern-day vehicle inspection tools help in the following ways to reduce the comeback costs:
- Double-check repairs
The aim of using digital vehicle inspection tools is to ensure no follow-ups are required. The series of steps is defined by the technician, who is well-trained to use advanced tools. At every step, a digital sign-off is required (for verifying the inspections). Hence, leading to a quality control system.
Let’s say a car’s brake was repaired, the vehicle inspection tool can signal a follow-up or suggest a second opinion by the expert on-premise.
This eliminates the likelihood of missing a crucial step during repair.
- Tracks the repairs
Using digital inspection tools allows auto shop owners to track the diagnostic codes and even keep vehicle data stored. The whole repair history is stored in the cloud, which allows technicians to view a vehicle’s history.
Also, the service managers can share the reference to past work done, analyze and identify the recurring and new issues, and also pinpoint any breakdown that might occur.
- Maintains documentation
Maintaining documents manually can lead to errors and data omission on a busy day. Because vehicle inspection tools are cloud-based, inspection details are easily recorded and stored in the cloud.
It can include videos, pictures, paperwork, technician notes, time stamps, estimates, and other details. All records and documents are verified as each step is performed during the inspection. It helps to avoid any disputes, miscommunication, and warranty claims.
- Improves customer communication
One of the major reasons for a comeback is the lack of proper communication between the customer and the technician. Verbal communication may not be their strongest skill, which is why inspection reports can be shared with the client that list the vehicle details.
Customers can be given real-time updates in case any further repair is required or a comeback is needed.
- Holds the technician accountable
The technician handling the repairs and inspections is initially accountable for the comeback. It makes the most sense to deduct the hours in the week when the comeback repair is expected. Vehicle inspection tools enable auto shop owners to eliminate broken workflows and keep an eye on mistakes.
In such scenarios, mistakes are traced to the technician who inspected the vehicle. This also encourages them to repair or inspect the vehicle properly the first time so that standards are met.
Modern-day inspection tools are worth every penny
Eliminating delays, correctly diagnosing the issue in the vehicle, and maintaining documents are the most important to a repair shop. You can create a quality control system using modern tools to ensure comebacks are reduced and increase customer retention over time.
Alex Morgan is an automotive technology writer with over a decade of experience covering innovations in vehicle diagnostics and repair solutions. Passionate about helping workshops improve efficiency and customer satisfaction,
View all articles